In the ever-evolving landscape of window manufacturing and sealed unit production, the importance of selecting the right warm edge spacer cannot be overstated.
As Mark Hickox, Sales Director at Thermoseal Group, points out, ensuring the correct specification of warm edge spacers is crucial in preventing premature insulated glass (IG) unit failure, which can lead to significant remedial costs for manufacturers and installers alike.
Understanding the Risks of Incorrect Specification
The thermal dynamics within a sealed unit can be complex. Mark emphasizes that a substantial increase in temperature—from a moderate 20°C to an extreme 80°C—can drastically affect the performance of spacer bars. “A spacer bar with a high linear expansion rate could cause the unit to fail prematurely,” he warns. This risk is exacerbated as sealed units become larger and as global temperatures rise.
For instance, a spacer bar in a 2-meter-long sealed unit could expand by as much as 16.92mm during daylight hours. With the ends of these bars fixed, such expansion can lead to significant bowing, akin to a rainbow, which forces the panes of glass apart. This mechanical stress can ultimately compromise the Polyisobutylene (PIB) sealant, allowing moisture to infiltrate the unit and precipitating failure.
The Shift from Aluminium to Rigid Plastic Spacers
In recent years, the industry has seen a shift from traditional aluminium spacer bars to rigid plastic alternatives. While this transition has its advantages, it has also introduced new challenges. Mark notes that inadequate attention has been given to the plastic compounds used in these spacers, which can lead to increased risks of failure.
Thermoseal Group’s Thermobar rigid spacer bar, composed of 40% glass fiber, offers a significant improvement over conventional aluminium spacers. This enhanced composition reduces the coefficient of linear expansion, thereby mitigating the risks associated with temperature fluctuations. However, not all rigid spacers are created equal. Some competitors have introduced products with little to no glass fiber content, or only 20% glass fiber, which can result in greater expansion compared to aluminium, especially in south-facing installations.
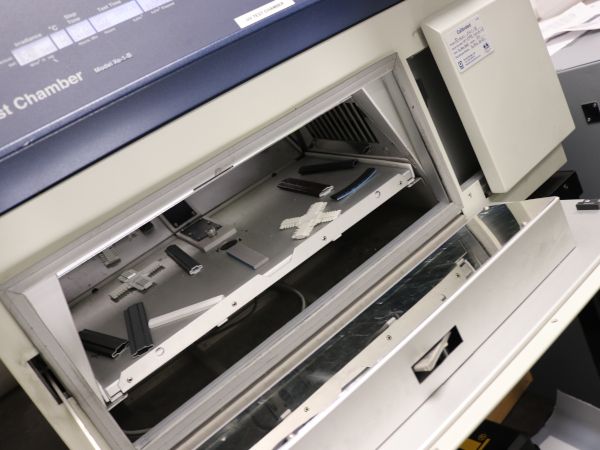
Beyond Linear Expansion: The Importance of UV Stability
Linear expansion is just one of many challenges that sealed units face, particularly as more cost-effective IGU components enter the UK market. UV stability is another critical factor that Mark highlights. Once installed, sealed units are subjected to various environmental stresses, including sunlight, heat, and moisture.
To address these concerns, Thermoseal Group has made significant investments in testing facilities, including a Q-Sun test chamber designed to simulate and accelerate the effects of the sun’s rays on their products. Each component—spacer bars, corner keys, and Georgian bars—undergoes rigorous testing to ensure that they maintain their physical integrity and aesthetic appeal over time.
Mark emphasizes that “we don’t want to see the product’s physical properties degrade, which could cause the unit to fail.” This commitment to quality ensures that not only do the components retain their color, which is increasingly important to homeowners, but they also perform reliably throughout the lifespan of the unit.
Comprehensive Testing for Long-Term Performance
By supplying a complete range of IGU components, Thermoseal Group is uniquely positioned to test these components in conjunction to confirm their long-term capabilities. As part of the Fenzi Group, they offer an extensive selection of IGU components, all guaranteed to perform effectively for the lifetime of the unit and beyond.
In conclusion, the correct specification of warm edge spacers is a fundamental aspect of insulated glass unit manufacturing that cannot be overlooked. With the potential for significant financial repercussions due to premature IG failure, window companies and sealed unit manufacturers must prioritize the selection of high-quality components, such as those offered by Thermoseal Group. By investing in advanced testing and quality assurance, Thermoseal Group not only safeguards the integrity of their products but also supports the broader industry in delivering reliable and durable sealed units.
Source:Thermoseal Group with additional information added by GlassBalkan