Glass processor companies are facing increasing pressure to comply with more stringent safety regulations and to meet the growing demand for laminated safety glass (LSG). In response to these challenges, HEGLA has introduced a new laser diode heating system that promises to deliver a range of benefits to glass processors. This new technology has been incorporated into the ProLam LSR series equipment for just under three years and offers four key advantages.
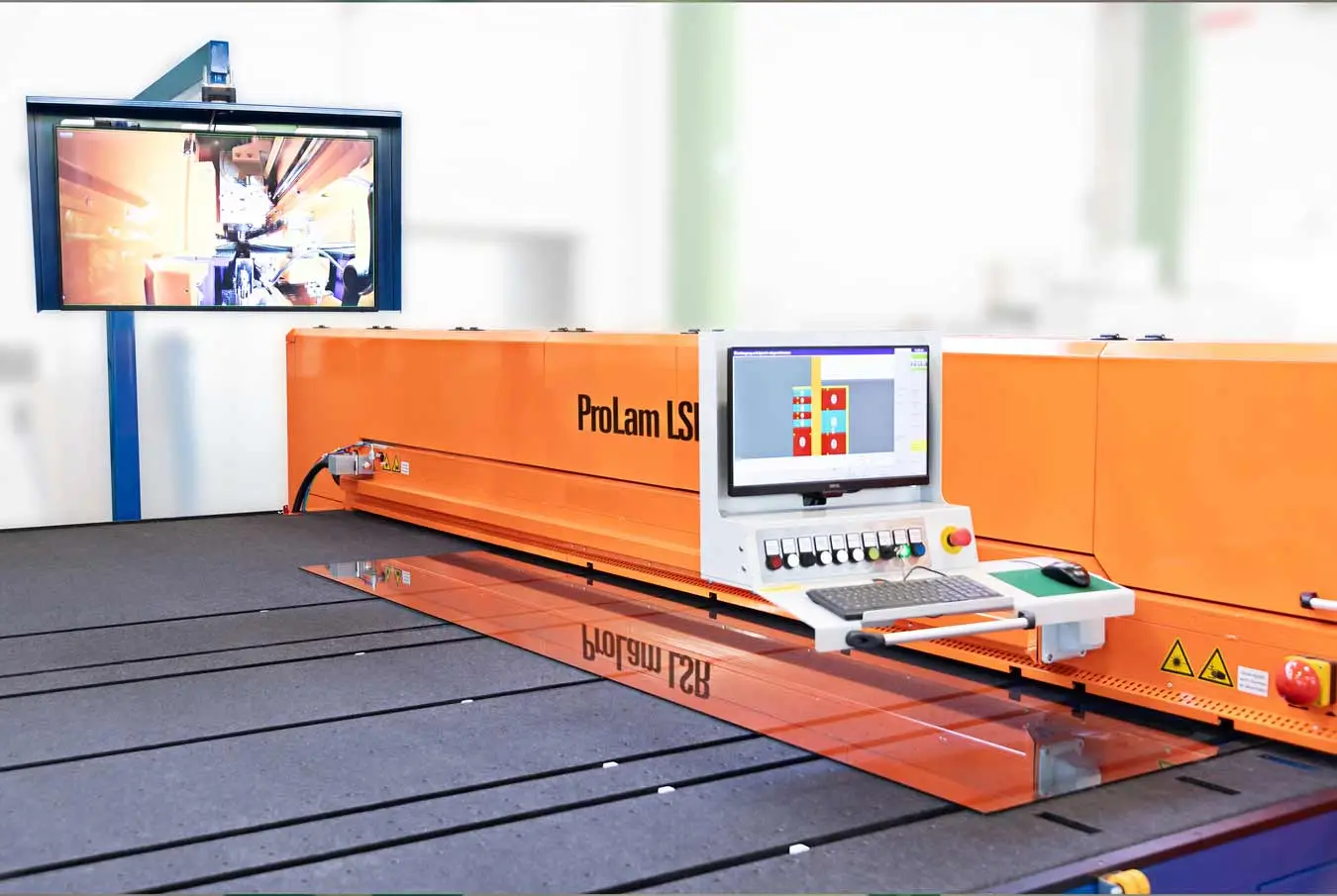
Focussed heat application shortens the cutting process by 20%
The heart of the new process is a patented laser diode heating system that replaces conventional heating tubes. The laser diodes are designed to consolidate the thermal energy of the laser, focus it on the scoring contour and apply it precisely to the film. This process enables the film to reach the required transformation temperature much faster than traditional techniques, resulting in a 20% reduction in cutting time. The diode strip is mounted in a fixed position above the cutting area, which saves time and allows the timing of the individual processing steps to overlap, accelerating the overall process.
No waiting for the next cuts
The use of LSR technology results in lower heat loss into the surrounding pane and air. This feature offers two additional benefits that are even greater than initially expected. Firstly, even when cutting thicker units, the glass only becomes warm to the touch at the edges, meaning that customers can move straight on to their next cut without waiting for the glass to cool down first. Secondly, tests have shown that the remaining laminate remains unchanged by the local application of heat, reducing the previous causes of subsequent delamination to a minimum.
High-quality glass edges
The precise application of heat energy and zero-offset dual cutting heads yield high edge quality without delamination. Consolidating the laser’s thermal energy also offers another benefit in terms of edge quality. When the glass is pulled apart, only the heated film in the cut is stretched, resulting in high-quality edges.
Shorter boot-up time saves energy
The laser diode strip is divided in half, and each side is activated completely or partially depending on the length of the cut, saving energy. The shorter boot-up time also improves the system’s carbon footprint. Additionally, the diode strip has proven to require less maintenance and be more durable than conventional technology, even after 20,000 operating hours.
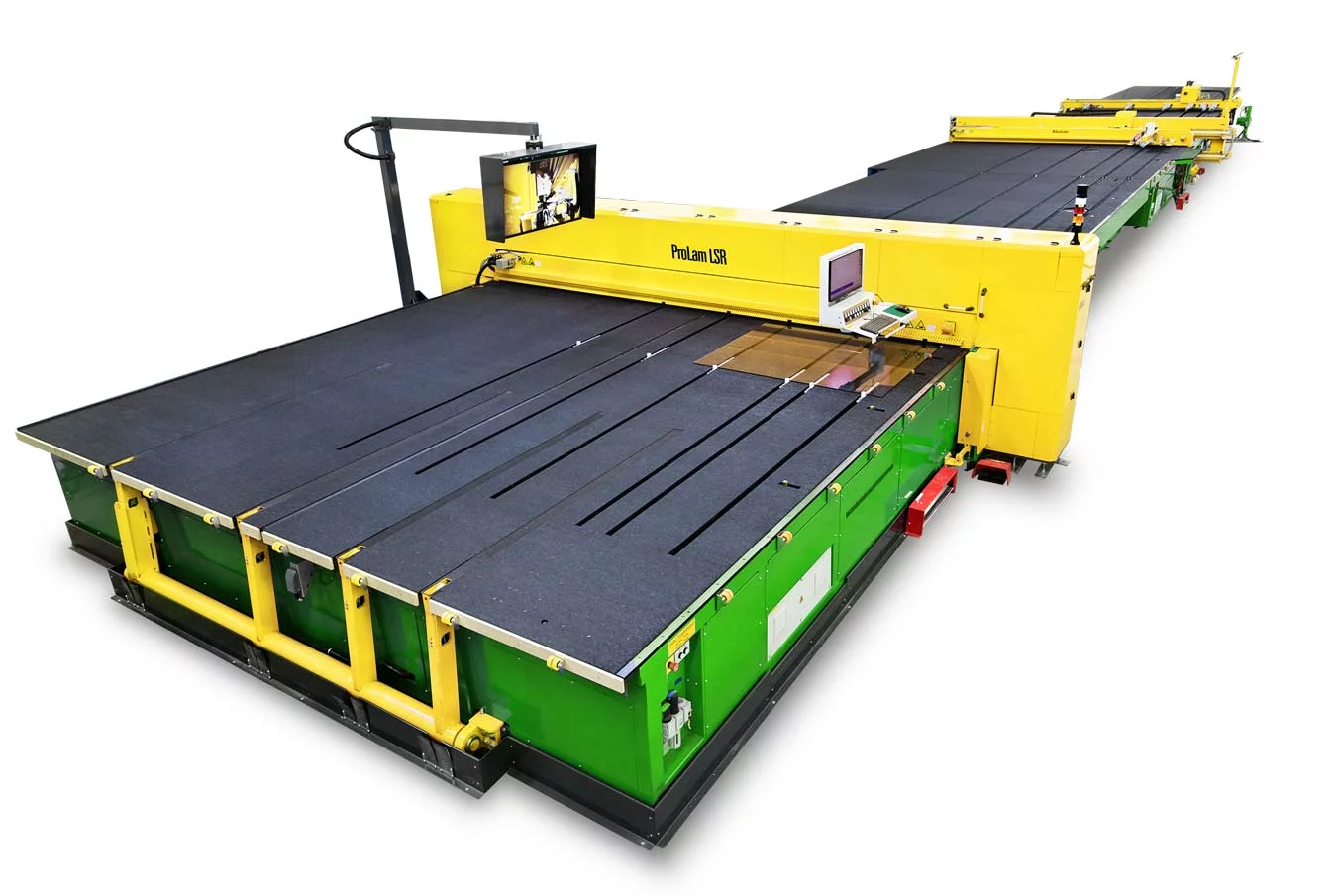
Adjustable to suit specific needs
The ProLam LSR comes equipped with the laser diode heating system as standard, and some existing systems in the ProLam series can also be retrofitted. Other features, such as the Kombi variant with automatic edge deletion, a float cutting head, and built-in breakout bars, add to the range of functions on offer. HEGLA also offers non-destructive laser printing to give glass a bespoke, machine-readable marking. This technology can be used for purposes such as triggering process steps during production, tracking workflows across the entire product life cycle, and reading the glass data using a scanner.
In conclusion, the new laser diode heating system is a game-changer for glass processors. It offers faster cutting times, higher cutting capacity, and improved edge quality while saving energy and reducing maintenance needs. These benefits make it an essential tool for any company looking to increase productivity and meet the demands of a rapidly evolving market.
Source: HEGLA GmbH & Co. KG with additional information added by GlassBalkan.