Revolutionizing Quality Control: Isophon’s Success with Sparklike’s Automated Insulating Gas Measurement System
Isophon Glas has experienced tremendous success since implementing the state-of-the-art Sparklike Laser Integrated™ automated insulating gas measurement system in their IG-line. Recognizing the growing importance of meeting customer demands and maintaining exceptional quality, Isophon made the strategic decision to invest in Sparklike Laser Integrated™ two years ago. Now, let’s hear from Mr. Özcan at Isophon to gain insights into their remarkable journey over the past two years.
Accurate Measurement for Superior Quality
Isophon has always delivered high-quality products, and to further ensure excellence, they incorporated the Laser Integrated system into their IG-line. This automated gas measurement system, along with the Sparklike Laser Portable device for gas concentration testing, has significantly improved their quality control process for insulated glass units (IGUs). Mr. Özcan explains that while the Laser Portable is still used for verification and double-checking, the Laser Integrated system provides reliable and precise measurements within the desired accuracy.
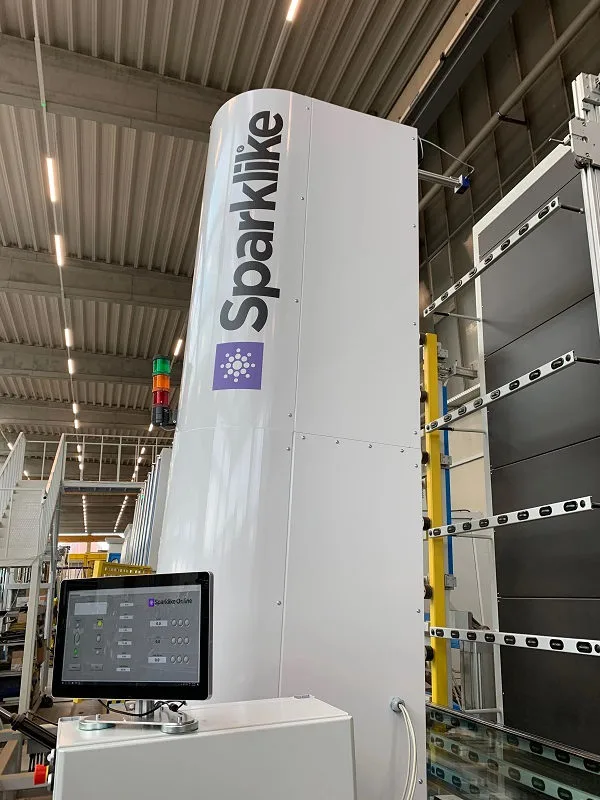
A Successful Investment Transforming Daily Operations
The Laser Integrated system has become an integral part of Isophon’s production process, allowing for immediate intervention if the gas filling level falls short. This real-time monitoring capability has proven invaluable to Mr. Özcan and his team. Additionally, the system has optimized the performance of their gas filling equipment, serving as an indicator of the filling machine’s functionality. With its ability to identify deviations and adjust processes accordingly, the Laser Integrated system has led to cost savings, increased production effectiveness, and improved overall efficiency.
Ensuring Safety and Complying with Energy Standards
For Isophon, investing in Sparklike’s automated insulating gas measurement system was driven by a commitment to safety and adherence to rigorous quality control standards. With a focus on minimizing risks and guaranteeing the required filling level for large projects with high-quality panes, Isophon views the system as a critical investment in their production process. Moreover, the system enables compliance with industry regulations and energy-saving standards, further reinforcing Isophon’s dedication to excellence.
Paving the Way for Future Innovations
Mr. Özcan anticipates that subsequent gas measurement and quality control in the installed condition will become increasingly widespread in the industry. This places greater emphasis on insulating glass manufacturers to integrate production control and documentation seamlessly. Fortunately, the laser system provided by Sparklike serves as an excellent solution, setting the stage for future advancements in measuring insulating gas concentration.
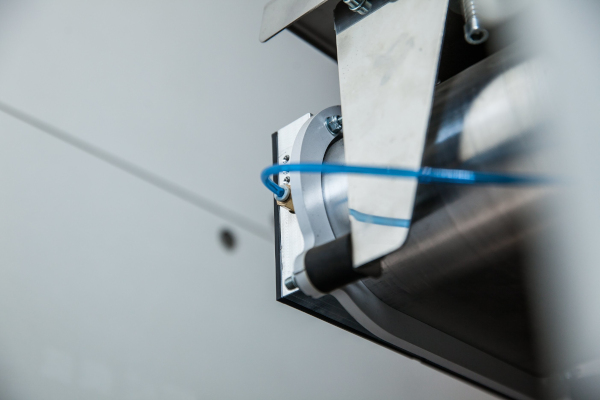
In Collaboration with Sparklike Distributor Rottler und Rüdiger und Partner GmbH
This interview was conducted in partnership with Sparklike’s trusted distributor, Rottler und Rüdiger und Partner GmbH, emphasizing their dedication to delivering cutting-edge solutions and outstanding customer support.
At Isophon, the Sparklike Laser Integrated system has transformed their quality control processes, enabling them to meet evolving customer expectations, enhance productivity, and prioritize safety. As the industry evolves, Isophon remains committed to staying at the forefront of innovation, ensuring their production exceeds the highest standards of quality and reliability.
CONTACT US TO TALK ABOUT YOUR IGU MEASUREMENT NEEDS
Source: By Jarno Hartikainen | Sparklike Oy with additional information added by GlassBalkan