Informative article on strategies to minimize costs in insulating glass production, written by Uwe Risle.
The article discusses how the rise in float glass prices due to high energy consumption in production has caused a drastic increase in the production costs of insulating glass. To stay competitive, IG producers need to optimize all steps of the production process to reduce the total cost of ownership (TCO).
Glass washing and drying
One of the most energy-intensive steps in IG production is the glass washing and drying process. IG manufacturers can reduce energy consumption by up to 25% by using the latest washing and drying machines that automatically switch off the drying zone as soon as the glass plate is dry and left this section. Moreover, by using a closed water circuit with a disc filter system, water consumption can be reduced by up to 15 times the current rate.
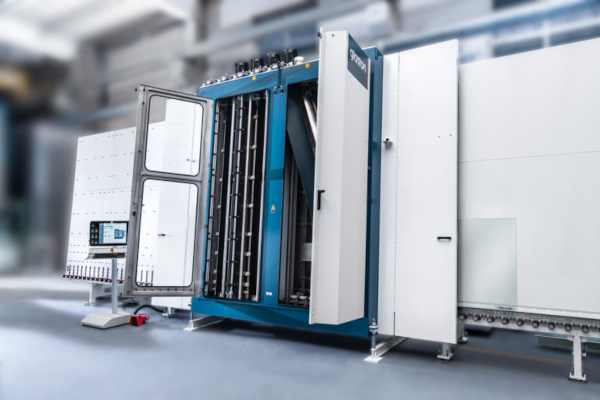
Conveyor systems
Roller-driven conveyor systems are more energy efficient than air-cushion technology. However, with the high risk of glass scratching during the process, the costs of roller-driven conveyors are higher due to frequent glass quality issues. Therefore, using Glaston’s modern air-cushion conveyor technology, glass quality is not compromised, avoiding remakes or reputational risks.
Components
It is important to use efficient and state-of-the-art component motors and drives. By using shared drives in modern IG lines, only the conveyor units carrying glass at any specific moment will be running, reducing electrical power consumption significantly. During drive deceleration, kinetic energy should be converted into electrical energy and fed back into the network, allowing energy savings of up to 20%. It is also preferable if IG manufacturing equipment uses hydraulic and electric drives instead of pneumatic systems, which consume up to seven times less energy.
Top-level efficiency with TPS® technology
The most advantageous solution to improve energy efficiency in IG production is the Thermo Plastic Spacer (TPS®) system. IG manufacturers need only a single machine, TPS®’APPLICATOR, instead of several components to produce the IG units, eliminating the need for other production machines. TPS® system synchronizes several processes into one, making it possible to complete daily production earlier due to reduced cycle times. TPS® units have a 12% lower U-value and a 60% smaller linear heat transfer coefficient at the edge zone than IG units with conventional aluminum spacers, resulting in significant energy savings for end-users.
In conclusion, even small saving measures can make a significant difference in the IG production process. IG producers must focus on optimizing all steps of the process to reduce the total cost of ownership and stay competitive in their markets.
Source: Uwe Risle | Glaston Corporation with additional information added by GlassBalkan