3D printing is redefining how aluminium components are designed, produced, and delivered across multiple industries, from aerospace and automotive to defence and industrial tooling. Known for its lightweight, corrosion resistance, and excellent strength-to-weight ratio, aluminium is an ideal candidate for additive manufacturing.
The most commonly used alloys in 3D printing include AlSi10Mg, valued for its good thermal properties and weldability, and Scalmalloy, a high-performance aluminum-magnesium-scandium alloy developed by APWORKS (an Airbus subsidiary). These alloys enable the creation of highly complex, durable, and lightweight parts.
Industrial Leaders Pushing the Technology
Key players driving the aluminum 3D printing market include:
- EOS GmbH – A leader in industrial 3D printing, EOS offers metal 3D printers like the EOS M 290, compatible with AlSi10Mg powders.
- GE Additive – Through its Concept Laser and Arcam EBM platforms, GE is using aluminum 3D printing to produce components for jet engines and turbines.
- Desktop Metal – Their Production System P-50 enables mass production of aluminum parts using Binder Jetting, a faster alternative to laser-based systems.
- Norsk Titanium – Though focused on titanium, the company collaborates on aluminum initiatives, especially for aerospace-grade structural parts.
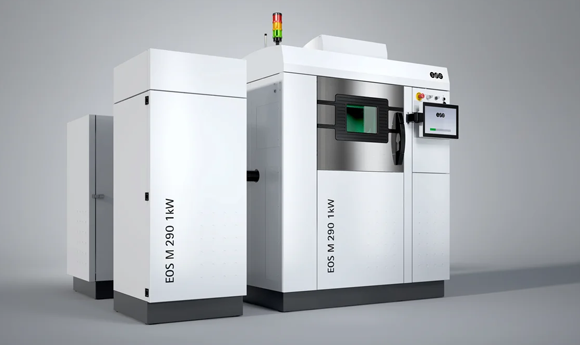
Applications Across Industries
In aerospace, aluminium 3D printing is used for brackets, housings, and heat exchangers, parts that require reduced weight without sacrificing strength. The automotive industry is adopting it for prototyping and custom parts, including performance vehicle components.
As additive manufacturing matures, aluminium’s role in 3D printing is expected to grow, driven by efficiency, sustainability, and design flexibility. With continuous advancements in materials and machine capabilities, aluminium 3D printing is no longer a future concept, it’s a current industry shift.
Source: Glass Balkan